Thermochemical conversions
Thermochemical conversion is another key process that uses heat to induce chemical transformations in the biomass constituents to produce energetically useful intermediate and/or end products.
Energy generation by combustion of biomass can be considered as the most archaic. However, increasing demand for transport fuels has led to the development of other processes that involve converting biomass into liquid and gaseous products such as gasification, pyrolysis and liquefaction.
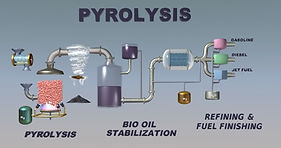
Pyrolytic properties of biomass are controlled by the chemical composition of its major components, namely cellulose, hemicelluloses and lignin and their minor components including extractives and inorganic materials. Pyrolysis of these materials proceeds through a series of complex, concurrent and consecutive reactions and provides a variety of products.
Pyrolysis cellulose at lower temperatures below 300° C involves reduction in molecular weight, evolution of water, carbon dioxide and carbon monoxide and formation of char. On heating at higher temperature 300–500° C, the molecule is rapidly depolymerized to anhydroglucose units that further reacts to provide a variaty of products and byproducts
Example: still higher temperatures, the anhydrosugar compounds undergo fussion, dehydration disproportionation and decarboxylation reaction to provide a mixture of low molecular weight gaseous and volatile produces. The composition of these produces and mechanism and kinetics of their production are reported Our review presents the summary of new studies on pyrolysis of biomass to produce fuels and chemical feedstocks carried out by our chemical engineers.
A number of biomass species, varying from woody and herbaceous biomass to municipal solid waste, food processing residues and industrial wastes, were subjected to different pyrolysis conditions to obtain liquid, gas and solid products. The results of various biomass pyrolysis investigations connected with the chemical composition and some properties of the pyrolysis products as a result of the applied pyrolysis conditions were combined. The characteristics of the liquid products from pyrolysis were examined, and some methods, such as catalytic upgrading or steam reforming, were considered to improve the physical and chemical properties of the liquids to convert them to economic and environmentally acceptable liquid fuels or chemical feedstocks. Outcomes from the kinetic studies performed by applying thermogravimetric analysis were also presented.
We can propose high standards plants and equipments with turn-key projects related to this tecnology from our industrial partners
In order to convert any Used Tyre & Plastic to fuel oil pyrolysis plant we can propose the following:
The Plant model 1
Raw Material that can be disposed, used tyres, waste plastic ,
Daily disposal capacity: 5Tons, 8Tons, 10Tons and 12Tons.
End products that can be got : fuel oil, heavy oil, residue or carbon, waste gas which will be re-heated during the process batch system.
Simple Process: Feeding-Cooling oil collecting-cleaning.
System included: Smoke dedusting system, Security System, Waste gas reburnt system , cooling system, electronic control system.
There are some questions:
That we would like to confirm from you:
1. What's the raw material do you plan to dispose?
The oil yield will be different for different raw material
2. What kind of end products do you expect to get?
For used tyre, plastic, the main output product will be fuel oil.
If you also consider to get diesel or gasoline, them you will need another distillation.
What's your daily disposal capacity?
We can provide plants with capacities of 5Tons, 10Tons, 12Tons Please see image on right-side.
__________________________________________
Mobile CAST is our new power generation system, realible, economic and real smart solution for biomass disposal problems.
Easy for produce electricity in affordable way in two models version 10kw & 20Kw

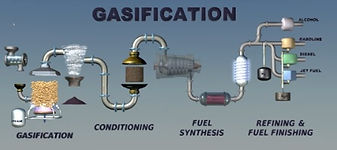
Gasification can be considered as Sustainable energy since is better than the direct incineration of biomass. This is a process that converts organic (biomass) or fossil based carbonaceous materials into carbon monoxide, hydrogen and carbon dioxide. This is achieved by reacting the material at high temperatures (>700 °C), without combustion, with a controlled amount of oxygen and/or steam. The resulting gas mixture is called Syngas (from synthesis gas or synthetic gas) or producer gas and is itself a fuel.The power derived from gasification and combustion of the resultant gas is considered to be a source of renewable energy if the gasified compounds were obtained from biomass. The advantage of gasification is that using the Syngas is potentially more efficient than direct combustion of the original fuel because it can be combusted at higher temperatures or even in fuel cells, so that the thermodynamic upper limit to the efficiency defined by Carnot's rule is higher or not applicable.
Syngas may be burned directly in gas engines, used to produce methanol and hydrogen, or converted via the Fischer–Tropsch process into synthetic fuel. Gasification can also begin with material which would otherwise have been disposed of such as biodegradable waste. In addition, the high-temperature process refines out corrosive ash elements such as chloride and potassium, allowing clean gas production from otherwise problematic fuels. Gasification of fossil fuels is currently widely used on industrial scales to generate electricity In essence, a limited amount of oxygen or air is introduced into the reactor to allow some of the organic material to be "burned" to produce carbon dioxide and energy, which drives a second reaction that converts further organic material to hydrogen and additional carbon dioxide. Further reactions occur when the formed carbon monoxide and residual water from the organic material react to form methane and excess carbon dioxide (4 CO + 2 H2O --> CH4 + 3 CO2). This third reaction occurs more abundantly in reactors that increase the residence time of the reactive gases and organic materials, as well as heat and pressure. Catalyst are used in more sophisticated reactors to improve reaction rates, thus moving the system closer to the reaction equilibrium for a fixed residence time.

Pyrolytic Plant model 1: Ten tons of daily disposal capacity
_____________________________________________________

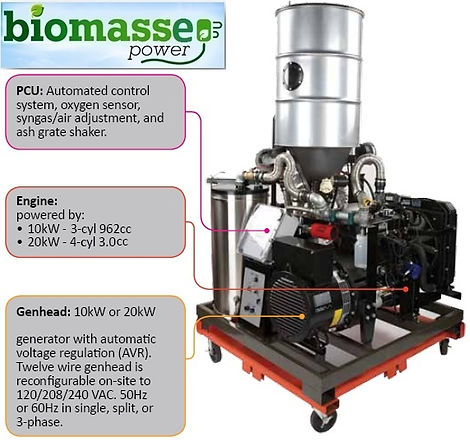
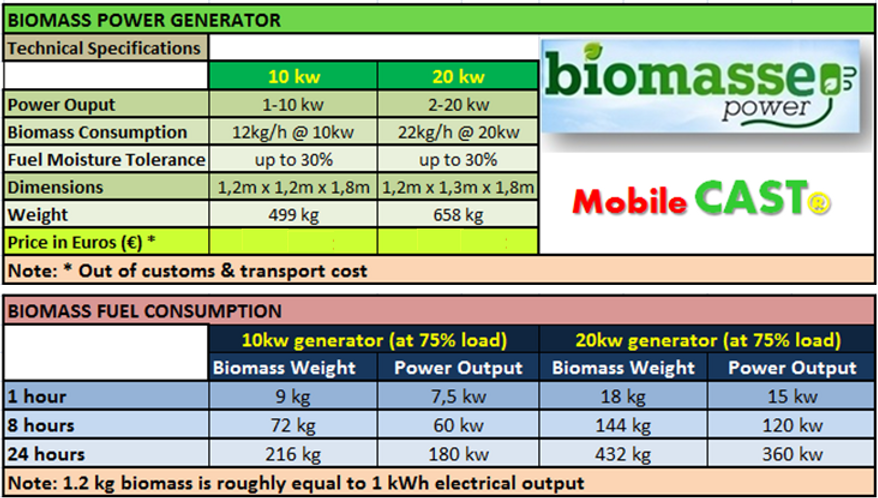